In today’s rapidly evolving manufacturing landscape, the ability to capture, analyze, and act on data in real-time is no longer a luxury but a necessity. A robust data platform serves as the backbone of modern industrial operations, feeding critical data points into the manufacturing process to enhance efficiency, reduce costs, and drive sustainability. According to Deloitte’s research, 98% of manufacturers have embarked on digital transformation initiatives, highlighting the sector’s commitment to leveraging digital tools for smarter operations.
Real-time data is the key enabler of intelligent automation, allowing manufacturers to manage production lines, predict equipment failures, and enhance product quality with unparalleled precision. Predictive analytics has also emerged as a game-changer, enabling companies to navigate machine failures before they occur, significantly reducing downtime. As manufacturing transitions further into Industry 4.0, companies that build strong data foundations will be best positioned to harness AI-driven automation, ensuring not only immediate process improvements, but also long-term scalability and competitive advantage.
This blog explores the pivotal role of data in helping manufacturers gain deeper operational insights while laying the foundation for AI and automation-driven transformation.
Cloud-based data
The Cloud offers centralized data management, interoperability, and real-time processing capabilities. These platforms enable manufacturers to aggregate data from disparate sources, including enterprise systems and production lines, into a single, accessible environment. By breaking down silos and integrating machine learning capabilities, manufacturers can generate actionable insights that improve production efficiency and product quality.
The partnership of 3M with Microsoft Azure SQL Edge demonstrates this transformation in action. A global manufacturer specializing in tens of thousands of products from safety apparel to office stationery, a 3M manufacturing plan used data integration from two separate production lines for predictive anomaly detection and reduced downtime. Azure IoT Edge processed real-time sensor and operational data locally, minimizing reliance on network connectivity. As a result, plant engineers could act on insights immediately, boosting efficiency without needing constant cloud access.
Scale and scale more
Scalability is a critical advantage of cloud-based platforms. Traditional on-premises systems struggle to handle increasing volumes of production data, often requiring expensive hardware upgrades. Cloud solutions, on the other hand, offer flexible infrastructure that grows with operational needs. Companies can scale resources up or down based on demand, reducing costs while ensuring consistent performance.
McKinsey’s analysis of digital manufacturing highlights how cloud-based platforms bridge operational disconnects by providing a unified digital thread across global operations. Manufacturers leveraging cloud data storage, analytics, and automation report improved decision-making and production agility. Companies implementing cloud-based AI systems saw marked reductions in machine downtime and increased throughput due to real-time monitoring and process adjustments.
The future at your fingertips
Predictive analytics transforms manufacturing from reactive to proactive operations by identifying trends and anomalies before they lead to failures. By leveraging historical and real-time data, predictive models can forecast machine breakdowns, optimize inventory levels, and improve supply chain logistics.
At 3M, predictive analytics enabled early identification of production anomalies, reducing unplanned maintenance costs and minimizing disruptions. By running machine learning models on Azure SQL Edge, 3M could detect potential failures hours before they occurred, allowing teams to take preemptive action.
AI-powered analytics thus improve decision-making by providing precise, data-backed recommendations. These insights allow companies to optimize production schedules, reduce material waste, and increase asset utilization.
McKinsey’s research indicates that manufacturers employing predictive analytics experience significant improvements in overall equipment effectiveness (OEE). By incorporating AI-driven forecasting models, companies allocate resources better, resulting in lower inventory carrying costs and improved on-time deliveries.
Sustainability at hand
By leveraging real-time data processing and AI, manufacturers can significantly reduce energy consumption, improve inventory management, and enhance equipment longevity.
- Sustainability
Cloud platforms enable energy optimization by monitoring real-time power usage across production lines. 3M’s implementation resulted in substantial reductions in energy waste, optimizing power allocation across machinery. Similarly, McKinsey’s findings show that manufacturers integrating predictive energy analytics achieve marked cost savings in utilities. - Demand planning
AI-driven predictive models allow manufacturers to adjust production dynamically based on real-time demand signals. By analyzing historical sales data and market trends, cloud-based solutions help companies minimize overproduction, reduce inventory costs and avoid both stockouts and overstock scenarios.
How Fortude is powering the future
In today’s fast-evolving industrial landscape, data is at the heart of intelligent decision-making. Fortude is at the forefront of this transformation, enabling manufacturing companies to harness the power of data for greater efficiency, agility, and scalability.
A leading global apparel manufacturer sought to modernize its data infrastructure to improve its operations. The company partnered with Fortude to implement a comprehensive data platform powered by Microsoft, AWS, Databricks, and Snowflake. This robust ecosystem integrates vast amounts of operational data, reducing the time required to derive insights while also pointing to areas that could benefit from automation.
- Build and unify
One of the biggest challenges manufacturers face is fragmented data, often stored in siloed legacy systems that limit visibility and efficiency. Fortude addresses this challenge by designing and deploying cloud-based platforms that consolidate data across the entire production lifecycle. By putting in place a solid analytics platform, Fortude enables the manufacturer to gain near real-time insights into the supply chain, production bottlenecks, and delivery timelines.
For the apparel manufacturer, the analytics platform helped for example with getting material status updates, which previously required extensive manual effort. This has enabled procurement teams to make proactive decisions. Enhanced visibility ensures fewer production delays and optimized resource allocation, leading to cost savings and improved operational resilience. - Scale and grow
Manufacturers often struggle with legacy systems that cannot scale with growing demand and business expansion. This was the case for the global apparel manufacturer. Initially, they received fewer orders in larger volumes, but the move to the cloud enabled them to expand their geographical footprint while efficiently managing increased capacity.
Expansion into international markets also presented logistical challenges for the apparel company, from managing multiple suppliers to ensuring consistent production quality, and on-time delivery. With Fortude’s support, the company implemented a unified analytics platform that connects all manufacturing systems under a single source of truth (SSOT). This transition has tripled operational visibility and streamlined cross-border supply chain coordination, positioning the company for continued growth.
Fortude’s expertise in building end-to-end data ecosystems helps manufacturers move toward Industry 4.0, where real-time data, AI insights, and cloud computing drive efficiency, sustainability, and innovation.
In leaps and bounds
As we look ahead, we also see technology set to become mainstream with the right data foundations in place. Among them are digital twins — virtual replicas of physical production systems — which are an exciting new development that is rapidly transforming manufacturing. By simulating real-world processes, manufacturers can test models before implementing changes, thereby reducing risks and costs. These AI-driven models offer real-time visibility into operations, helping companies proactively address inefficiencies and improve performance.
The future of manufacturing will similarly be autonomous. Machine learning models will continuously analyze data to refine production workflows, allocate resources more efficiently, and automate decision-making. The integration of AI into manufacturing ecosystems will drive:
- Smarter supply chains that self-adjust based on market conditions.
- Autonomous production lines that dynamically respond to real-time data.
- AI-powered quality control to detect and rectify defects before they impact final products.
As these technologies continue to evolve, drawing on the benefits of quantum computing to come, manufacturers must be ready to adopt and innovate to stay competitive in ever-volatile markets. With the right data strategy in place, the manufacturing industry is poised for a new era of intelligent, efficient, and sustainable operations.
FAQs
By capturing and analyzing real-time data, manufacturers can optimize production, predict failures, and improve product quality. A strong data platform enhances operational visibility, allowing for smarter decisions and proactive management of resources, ultimately ensuring competitiveness and scalability in today’s fast-paced market.
Cloud platforms enable manufacturers to centralize and manage data from diverse sources, breaking down silos. They provide real-time processing and seamless integration with machine learning, allowing for actionable insights across the production cycle. The cloud’s scalability ensures that data storage and analysis grow with business needs, enhancing operational efficiency, decision-making, and cross-functional collaboration.
Predictive analytics in manufacturing forecasts machine failures, optimizes inventory, and enhances supply chain logistics. By analyzing historical and real-time data, predictive models help prevent costly downtime and improve resource allocation. These insights enable proactive decision-making, leading to better equipment utilization, reduced waste, and improved operational efficiency, which ultimately contributes to increased throughput and cost savings.
Fortude helped a global apparel manufacturer modernize its data infrastructure by implementing a data platform powered by Microsoft, AWS, Databricks, and Snowflake. This solution unified data from various sources, providing real-time insights into production, supply chain, and delivery timelines. The platform improved decision-making, minimized delays, and enhanced operational resilience, positioning the company for growth and scalability.
Subscribe to our blog to know all the things we do
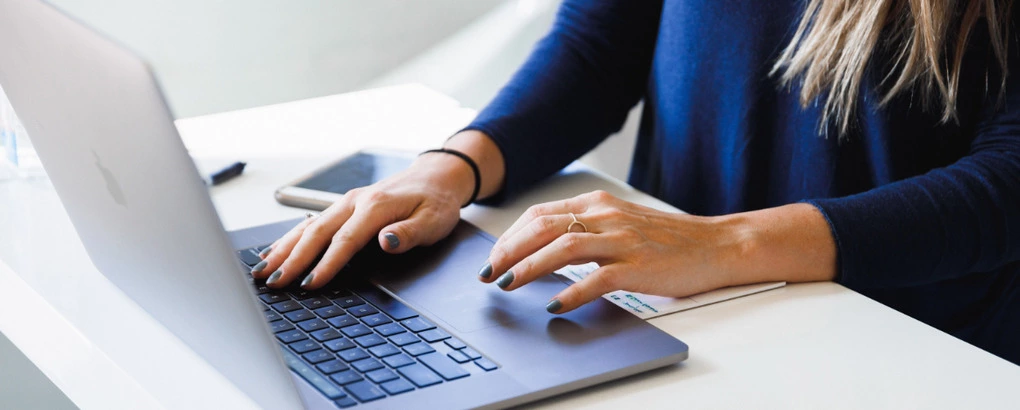