Infor M3
A leading UK-based industrial manufacturer turns to Infor M3 to manage regulatory compliance
Infor M3
A leading UK-based industrial manufacturer turns to Infor M3 to manage regulatory compliance
Download Case Study
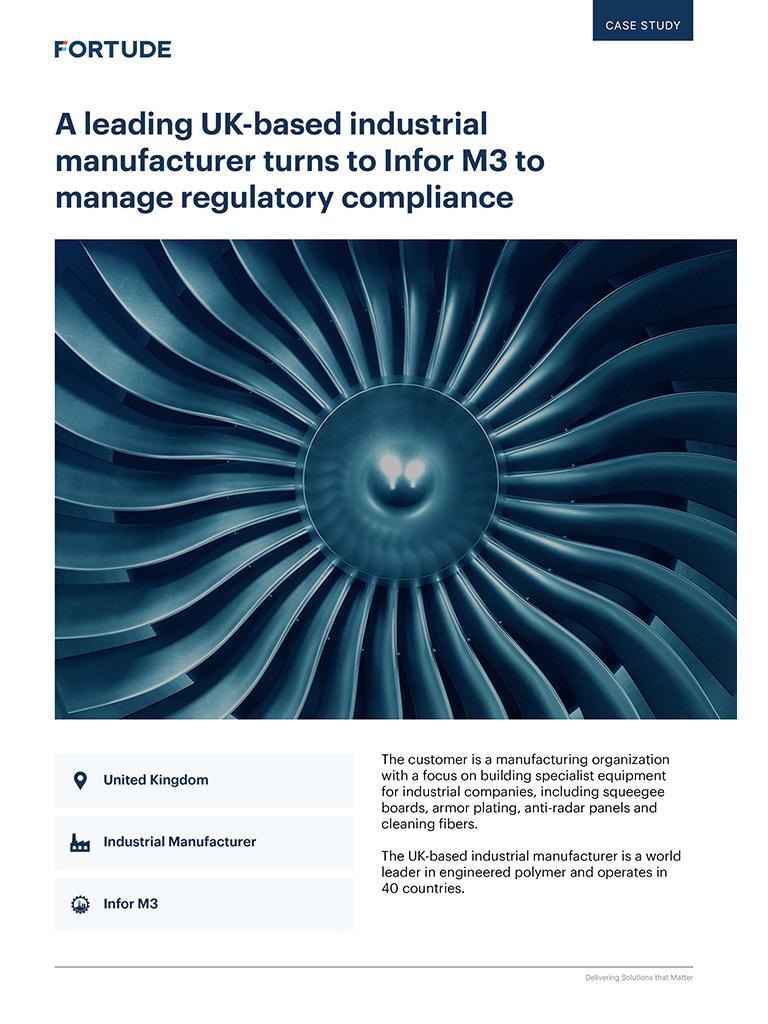
Subscribe to our blog to know all the things we do
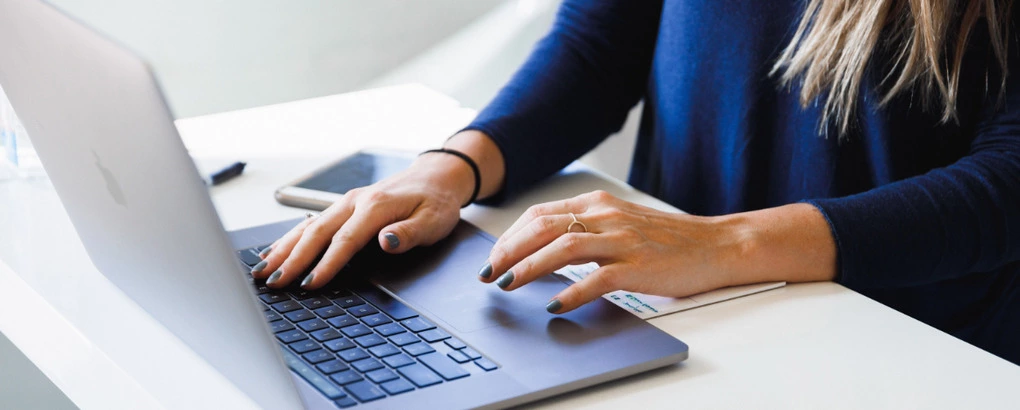