Infor M3
Australian ready-made meals manufacturer nails recipe for success with Infor M3
Infor M3
Australian ready-made meals manufacturer nails recipe for success with Infor M3
Download Case Study
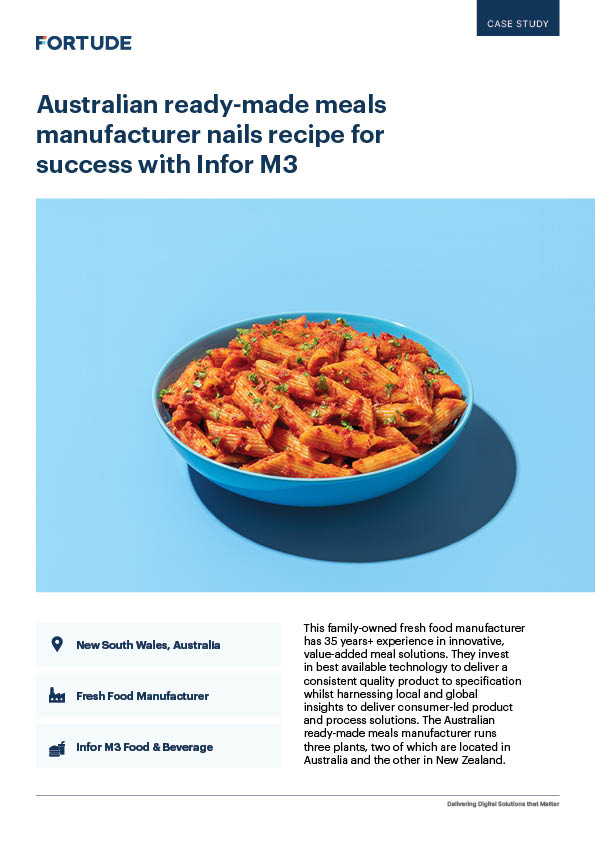
Subscribe to our blog to know all the things we do
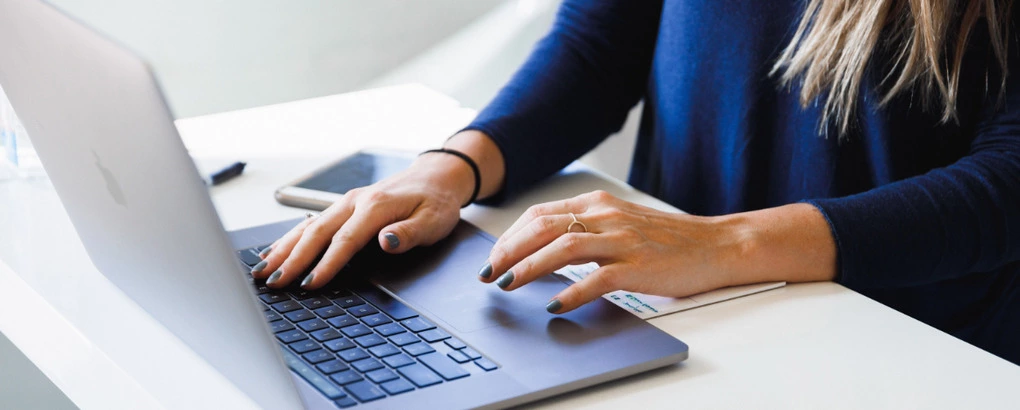