A lot on the plate
How can food and beverage manufacturers survive, compete, and thrive in a world of shocks?
It’s been one disruption followed by another these past few years – global shutdowns, supply chain crises, and rising food prices. Every single one of these events and their after-effects required agility, foresight, and new thinking faces yet another issue – an aging workforce, and resulting labor shortages for manufacturing (particularly in industrialized countries). For example, the US alone will have over 2.1 million vacant manufacturing jobs by 2030, according to one estimate. There’s also a growing number of environmentally conscious consumers to contend with.
To answer our question, we take a look at two very different, fictitious food and beverage manufacturers and compare what possibilities open up for them once they leverage the digital technologies of the Industry 4.0 era – and what constraints they risk facing should they choose not to. Incorporating new and emerging technologies, such as artificial intelligence (AI) and machine learning (ML), the Internet of Things (IoT), robotics, blockchain, cloud, and edge computing, into manufacturing processes does not stop with the creation of more efficient, ‘smart’ factories. Through digital transformation, manufacturers stand to gain the much-needed means to respond to unpredictability and strategize for new.
Adoption of these technologies in the food and beverage industry stands at 20-40% (much lower compared to other industries), so it seems like the industry is only getting started. But what if you choose not to adopt digital solutions? Here’s how far back in time you would be taking your business? Let’s find out how two fictional manufacturers with different approaches to digital technology will navigate uncertainty.
The tale of two food and beverage manufacturers: Stuck in the past vs. Future-ready
- The factory of the past
Everfresh Creations is hesitant to adopt technology. Like many other manufacturers in the industry, this manufacturer mass produces daily household food and beverage items to meet growing consumer demand. Any time there is a labor shortage, production processes are delayed, resulting in slower output. Activities that are integral to successful operations, such as forecasting consumer demand, quality control, machine health, production levels, and maintaining inventories, are largely manual tasks. These often lead to compromises in the quality of the end products, higher possibilities of product recalls or defects, an inability to respond to fluctuating market demand quickly, and incomplete knowledge about production processes.
Everfresh has a fragmented supply chain as well. With supply chains being spread across several countries and geographic regions, how can this manufacturer keep up with all the updates related to raw materials, suppliers, packaging providers, warehousing, and logistics? And then there’s the sustainability factor. Reaching sustainability goals is much more difficult because there is no real-time data about production levels and food storage conditions. This leads to overproduction and more expired or damaged products ending up in landfills. Managing energy consumption, too, remains a challenge without the means to track this data.
This is a less-than-ideal situation for any manufacturer.
But let’s take a look at another kind of food and beverage manufacturer – one that understands where the world is heading with Industry 4.0 and the pressing need to explore technologies such as automation, IoT, AI-driven data analytics, cloud solutions, and blockchain.
- The essential transformation toolbox for a smarter food factory
Savor & Co. has automated its routine processes and even introduced industrial robots to address both labor shortages and introduce new products to the market faster. The latter is especially valuable in present times when inflation is changing consumer spending habits and food and beverage manufacturers must alter existing products or introduce new ones while keeping abreast of new developments. In this way, Savor & Co. will also join the growing number of industrial companies that plan to allocate 25% of their spending on automation over the coming years.
The manufacturer also utilizes an IoT solution to maintain high product quality and safety standards and monitors the efficiency of their operational processes. Sensors in factory machines generate data about machine health to aid this manufacturer in performing predictive maintenance on machines. These sensors can also generate data on energy consumption so that the manufacturer can make alterations to their processes if needed. Furthermore, sensors placed in storage areas can generate data on conditions such as temperature and humidity that have an impact on product quality. These can be altered to ensure optimal conditions so that fewer products are damaged due to poor storage.
Access to real-time data on supply chains and production lines, with comprehensive insights into possible delays, bottlenecks, and dangers, is yet another significant advantage of using digital technologies. This manufacturer can analyze the data generated to change processes that need changing for improved product design and innovation, and ultimately become more prepared to compete in today’s volatile market conditions.
Cloud-based platforms also provide the manufacturer with real-time information about inventory levels, function as a communication platform with all stakeholders throughout supply chains, and maintain up-to-date stock levels. It has also become an indispensable technology, if and when, the manufacturer decides to scale operations, as the data will be safe.
And finally, there’s blockchain. With its decentralized nature, blockchain can contribute to improving supply chain transparency. Savor & Co and its consumers have access to product information such as the source of origin, the production process, and full lifecycle of the product. For the manufacturer, there’s the added benefit of strengthening their quality control processes and introducing greater traceability of raw materials/items that do not meet their safety standards. This will help the manufacturer greatly, given the regulatory and public scrutiny of hygiene standards in the industry.
Everfresh Creation and Savor & Co. may operate in the same industry, but the differences between them are significant.
The road ahead
The answer to our original question, How can food and beverage manufacturers survive, compete, and thrive in a world of shocks?, is clear. Surviving, competing, and thriving in today’s ever-volatile world requires transitioning from being technology-averse to being digitally agile. Savor & Co. is better placed to understand consumer behavior, produce new products based on changing preferences, gain comprehensive insights into supply chains, automate labor-intensive tasks efficiently, align processes with their sustainability ethos, and monitor their impact on the environment. On the other hand, Everfresh Creations is unable to respond to shocks or keep abreast of competitors and, in time, will either be acquired by a more agile, future-oriented manufacturer (like Savor & Co.), or simply become irrelevant.
Digitally transforming the food and beverage industry is not solely about technology. It requires a holistic approach to understanding the long-term needs and challenges, selecting the most appropriate technology, choosing the right implementation approach, and creating a culture that’s conducive to change. Whether it’s automating processes or boosting supply chain traceability, Fortude works with numerous global food and beverage manufacturers to help them leverage technology in their operations. Find out how you can digitally transform your operations.
Related Blogs
Subscribe to our blog to know all the things we do
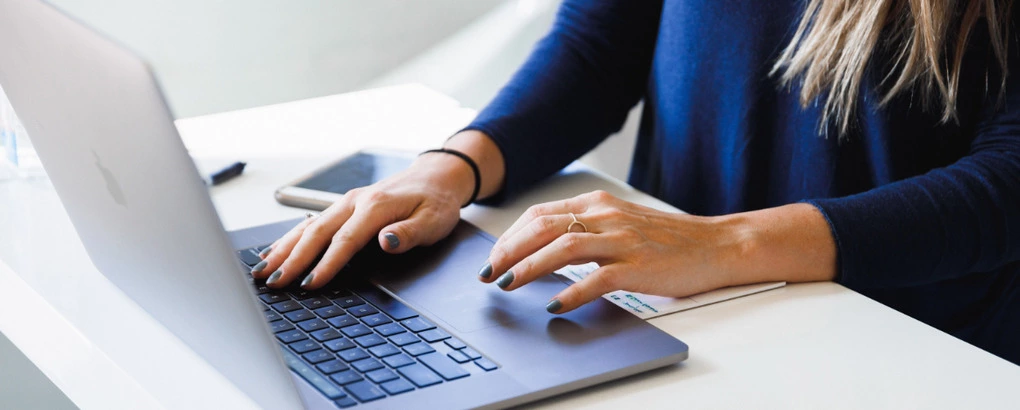