Here’s the scoop: a rapidly expanding world, demanding customers, siloed systems, inadequate supply chain management, and digital-savvy competition are putting immense pressure on distribution companies to simply keep up. These challenges require agile yet robust solutions. We’ve witnessed the increase of the C-suite’s interest in leveraging Enterprise Resource Planning (ERP) systems, and this is not merely a technical upgrade, but a strategic necessity to stay competitive.
For the distribution industry, ERP systems mean improved efficiency in avoiding supply chain disruptions, streamlined processes for warehouse and factory management, end-to-end visibility of each step of the distribution process and process optimization through technological advancements.
Given that ERP has gone through many iterations of development since its inception; beginning with the integration of several functional areas of a company, to eventually becoming mobile-enabled, and now incorporating artificial intelligence for business optimization, the benefits a business can reap have become numerous!
So, whether you aim to improve internal operations or reach the world through an enabling ERP, you might want to follow these key pre-implementation steps to mitigate re-strategizing or potential bottlenecks.
Identify pain points that need to be addressed
Before embarking on an implementation journey, it’s crucial to conduct a thorough analysis of the existing processes and pain points. Understanding these issues will help you set clear goals and align the project with the company’s strategic objectives. It will also give you the opportunity to assess the need for custom integration and smart solutions to optimize the functionality of specific business areas.
For example, your company could be facing challenges in managing international operations. This can cause inconsistencies in financial reporting, language and communication, and complications in handling international transactions. A suitable solution to this could be a multi-language and currency ERP designed for global distributors.
By identifying bottlenecks early on, you can weigh your ERP options and minimize risks that could potentially derail the project, once kickstarted.
This can be achieved by:
- Mapping out current processes by engaging all stakeholders to pinpoint specific issues and help the project team understand the nuances of each process. From procurement to order delivery, involve all stakeholders and showcase your interest in improving daily pain points. Not only will this provide you with invaluable insight, but it will also help employees embrace change – maximizing user adoption, post-implementation.
- Analyzing performance data such as Key Performance Indicators (KPIs) can help you gauge performance inconsistencies, and in return, implement ways to solve problems effectively. From inventory turnover to delivery times to customer satisfaction, metrics can highlight where you need to shift your focus.
- Identifying pain points through surveys and interviews will help you uncover issues that may not be evident from data analysis alone. One-on-one, in-depth chats will help employees communicate problems and allow the project team to understand the root causes of certain problems. Discussions with frontline employees can provide on-ground information that could otherwise be overlooked.
Define the scope of the implementation
Defining the scope of the implementation is important because it outlines what the ERP will provide and helps manage expectations. This helps an organization gain clarity and focus, aligning the project with company goals. Moreover, it helps with:
- Allocating resources effectively: be it budgeting, assigning tasks or scheduling timelines, all of which are crucial for staying on track and on budget.
- Mitigating risks: by identifying potential risks and better planning the implementation.
- Aligning stakeholders: by having a shared understanding of the project objectives, deliverables and even its limitations.
This is particularly important when operations involve several key figures and departments. From procurement to customer service, each person involved in the business must understand the change that is being implemented and how it affects their responsibilities; what matters will be resolved? And what requires their attention.
Migrate your data
Data is the backbone of any ERP system. Accurate migration of data can ensure that business operations run as usual without disruptions. However, there are several layers to ensure the accurate and clean migration of data. You may start by:
- Identifying data sources such as inventory management systems, order processing systems, CRM or accounting software.
- Deciding which data needs to be migrated. This typically includes master data (customers, suppliers, products), transactional data (orders, invoices), and historical data for analysis.
- Conducting a data audit to spot any errors such as data duplicates, outdated data or other inaccuracies, and cleaning the data thereafter.
- Establish a mapping between the fields in the old system and new system to ensure data is transferred to the appropriate fields.
- And develop a detailed data migration cutover plan that outlines the steps for the final migration, including timing, resource allocation, and contingency plans.
Think about customizations
While ERP systems come with a broad range of built-in functionalities, they might need to be tailored to meet unique needs of a business.
For example, customizations can help you integrate with barcode scanning systems to improve efficiency or support complex pricing modules – especially for e-commerce businesses that provide customer-based or seasonal discounts.
Not just that, tailoring the ERP to improve inventory tracking, automate replenishment processes, manage fleet and transportation, generate reports or uplift customer service can have significant positive impacts on a business.
Custom dashboards and reports can provide visual, actionable insights, and be scheduled to generate in a pace the business wishes.
We understand this is a lot to keep in mind. Speak to us at Fortude to find the best solutions for your business.
Give importance to change management and knowledge transfer
Preparing, supporting, and helping employees transition from old processes to the new ERP system is just as important as the rest of the tasks on the implementation pipeline.
A holistic change management initiative will ensure the new system is adopted smoothly and the expected benefits are realized. Like how pain points were discovered through stakeholder engagement, change management will help decision makers understand key changes in processes, roles and responsibilities.
Active participation and advocacy from senior management is crucial to drive change management efforts, not to forget training and support must be a continuous practice. This brings us to the importance of knowledge transfer.
What good use of a new ERP if your employees don’t know how to use it? Knowledge transfer ensures all users are well-equipped to utilize the system effectively. This involves training and sharing of critical information regarding the ERP and its capabilities. From warehouse staff, sales teams, and logistics personnel must understand how to handle inventory, process orders, and coordinate supply chain activities using the new system.
Role-based training sessions, hands-on workshops, and on-demand educational resources are needed to enable and empower the new users.
Knowledge transfer must be a sustainable and continuous process. Engage both internal and external SMEs for both targeted and holistic training.
Allocate time for testing
A crucial task in the pre-implementation process is the rigorous testing of the new ERP. Remember your objective is to make processes more efficient – not the opposite. So, test the ERP before going-live to stay ahead of potential breakdowns. This is best done by assessing the system’s functionalities, integrations and performance and identifying discrepancies – if any – through some of the methods mentioned below.
You may:
- Unit Test various components of the system to validate each module of the system are functioning as expected.
- Carry out User Acceptance Testing (UAT) to engage the end-user to make sure the new system aligns with their workflows.
- Regression Test to ensure new changes do not interfere with existing functionalities.
- Test overall business scenarios from order processing to financial transactions to ensure the ERP is functioning as intended.
With Infor M3 specific libraries for accelerated implementations and pre-built industry-specific test cases, our testing tool “Fortest” is ready to elevate your testing strategy to the next level.
Go live and maintenance
Now that you’re ready for go-live, ensuring the system stays up and running becomes a key component. Maintenance must be given equal importance with regular monitoring and user feedback for processes to continue as expected, generating real-time data. Continuous training and support make sure that your employees adapt to updates as well as fully leverage the ERP system’s capabilities.
Beyond this, it’s important to seek the support of your ERP provider to stay on top of industry standards and regulations.
Your business must grow with the ever-evolving world and so must your ERP. Enabling such business agility should be a top priority in the ERP implementation you undertake.
Our team of Infor M3 Certified consultants understand your Infor M3/CloudSuite application inside-out and can help you reduce IT operations costs and take the workload off your in-house team.
So, there you go; a 7-step checklist to tick off before you implement a brand-new ERP. You will now be able to respond to market demands quicker, manage each player in the supply chain, reduce operational costs, gain insights on how to elevate the customer experience and be on your way to being an industry leader!
Subscribe to our blog to know all the things we do
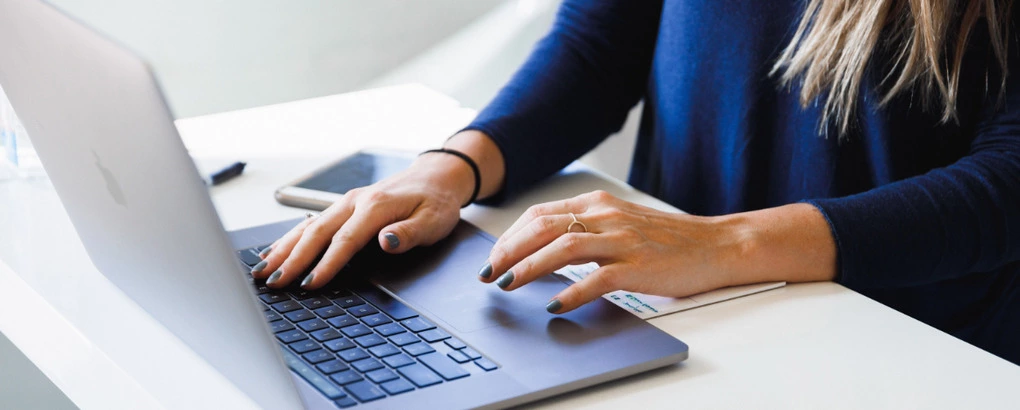