In this three-part blog series, John Broadbent, External Consultant at Fortude, explains how F&B manufacturers can do more with less while transforming business processes and services using digital technologies such as Industry 4.0.
Digital transformation (DTx) is upon us, affecting all aspects of our lives. When it comes to business itself, departments such as finance, HR, sales and marketing can all benefit from DTx.
How does manufacturing, especially manufacturing in the food and beverage sector stand to gain from DTx?
While DTx is a whole-of-business undertaking, one of the misconceptions around DTx is that all must be done at once. One of the first steps food and beverage business leaders must take is to set a DTx strategy that modernises the way data is created, collected and delivered.
Industry 4.0, in a nutshell, is the convergence of three underpinning technologies:
• Cyber-physical systems (CPS)
• Networks and cloud
• The Industrial Internet of Things (IIoT)
Cyber-Physical Systems refer to those systems with which we as human beings interact. Some examples are autonomous vehicles, smart electrical grids, autopilots and the typical information displays (human-machine interfaces or HMIs) found in manufacturing plants, which provide insight into processes, much like the dashboard in your car.
Networks include the associated infrastructure such as switches, firewalls, LANs, WANs and cyber-security, as well as connectivity to Cloud-based services. These form the second pillar of Industry 4.0.
Finally, the IIoT, a subset of the IoT (Internet of Things) collects data in a manufacturing environment. This includes robots, smart instruments, control systems (such as PLCs and SCADA), cameras, weighing scales—anything we can connect to a network and use to ‘mine’ data.
Think back 20 years and remember all the paperwork that occupied a typical F&B facility. Manufacturing orders were printed and handed to production people. Myriad special recording sheets were created and printed to capture important processes, and safety and quality information. Finally, finished goods were created and recorded manually, sometimes with manually printed labels for cartons and pallets. Often, hundreds of spreadsheets were created to support all of this.
Did you know a typical mid-sized F&B facility produces some 900,000 sheets of paper production records in a single year?
So how is DTx and Industry 4.0 changing that?
We can now mine cyber-physical systems or IIoT (edge) devices directly, use networks to collect their data in real-time, store them in on-premises or cloud-based repositories at a minimal cost, and then report on those results via real-time performance dashboards to a different strata of the organisation. All of this takes place in a completely paperless environment. This is the emergence of the ‘digital factory’.
Artificial intelligence (AI) systems can now help optimise production planning and scheduling, communicate with production machinery and then, monitor and capture real-time information on production performance, and ‘close the loop’ back to scheduling with expected order completion times based on the current production rate. The AI engine uses this updated information to continuously optimise the production plan and schedule, resubmitting it to the factory, achieving real-time alignment between planning, scheduling and production.
Approaches such as the above, increase the velocity and agility of the production environment, allowing food and beverage manufacturers to swiftly respond to changing conditions, such as supply chain issues, internal production issues, breakdowns and labour requirements.
This approach also reduces waste, increases efficiency, identifies bottlenecks, and makes the production environment much more visible, enabling root cause issues to be identified and addressed, further improving the triple bottom line.
If you are serious about becoming the F&B producer of choice, a solid DTx and Industry 4.0 strategy that allows you to do more with less and become highly efficient, is an absolute must.
An Industry 4.0 Perspective
The Digital Foundation for
Smart Manufacturing in Food & Beverage
A fireside chat featuring industry experts
Related Blogs
Subscribe to our blog to know all the things we do
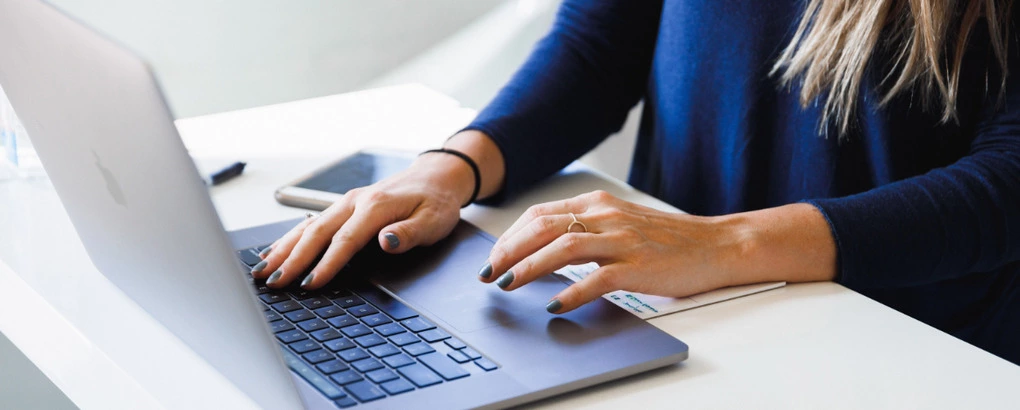