Digital twins, near-zero downtime, sustainable manufacturing, Generative AI assistants in manufacturing, and predictive maintenance.
The digital technology-enabled factory of today is very different from that of a decade ago. The manufacturing sector has been quick to adapt to this new reality. But while most manufacturers understand that technology holds significant promise for efficiency and resilience, some remain hesitant to fully embrace it. Primary concerns include perceived upfront costs, internal expertise gaps, and resistance to change.
Traditionally, integrating solutions from various vendors incurred large consultant fees. However, modern integrated platforms now offer user-friendly solutions with plug-and-play hardware, accommodating a range of budgets. Intuitive solutions like Microsoft Power Platform require no coding effort and facilitate upskilling of existing staff, while helping leaders build agility and resilience into their DNA. Fear of change is also a common hurdle, particularly among plant managers grappling with labor challenges amidst economic uncertainty. This blog explores how some leading manufacturers across diverse industries are leveraging low-code/no-code solutions like Microsoft Power Platform to navigate some of the biggest manufacturing challenges of today.
Navigating the manufacturing maze: Current and future frontiers
Currently companies encounter a host of challenges that demand attention and adaptability. From a shortage of skilled workers to intricate supply chain dynamics, the industry is navigating a complex terrain. The recent global health crisis and ongoing geopolitical tensions has only intensified these issues, amplifying labor shortages and highlighting the importance of digital proficiency.
Manufacturers are now faced with the urgent task of retaining talent and fostering digital literacy among their workforces. At the same time, supply chain disruptions persist, driven by factors such as rising raw material costs and logistical bottlenecks. Moreover, the increasing digitization of manufacturing processes has brought cybersecurity to the forefront, necessitating healthy risk management strategies.
In addition to these challenges, there is a growing emphasis on environmental sustainability within the manufacturing sector. Consumers are increasingly demanding socially responsible practices, prompting companies to integrate Environment, Social, and Governance (ESG) initiatives into their operations effectively.
Unleashing innovation: The Power Platform’s impact on manufacturing excellence
Microsoft’s Power Platform emerges as a crucial tool for addressing the industry’s intricate challenges amid these shifts. This comprehensive solution empowers developers and decision-makers to streamline operations, boost productivity, and foster innovation through low-code application development, automation, AI-powered chatbots and integration, and data-driven insights.
Featuring a range of essential components such as Microsoft Power Automate for task automation and intelligent automation, AI Builder’s prebuilt models for document processing, text generation, category classification, entity extraction, sentiment analysis and object detection, and Microsoft Power BI for data analytics and business intelligence, the Microsoft Power Platform offers manufacturers a tailored suite of tools. These tools are specifically designed to transition manual, labor-intensive processes into agile, efficient operations.
From ensuring quality control to managing employee training and safety protocols, the Power Platform provides a holistic solution to the diverse needs of manufacturing environments. Its user-friendly interface and integration with Azure services enable organizations to innovate effortlessly, addressing challenges in real-time and empowering their workforce to drive continuous improvement.
Take for example a leading apparel manufacturer in Asia that faced challenges with production efficiency and machine downtime. The absence of a comprehensive downtime tracking system hindered effective disruption management, resulting in productivity losses and operational inefficiencies. Fortude leveraged Microsoft Power Platform to develop a comprehensive system to enhance operational efficiency and minimize downtime. This solution included an Admin Panel to manage master data. The Power BI Dashboard provided real-time visualizations to monitor downtime patterns and make informed decisions. The Team Leads’ View enabled efficient breakdown reporting with a dedicated tablets near production lines for real-time data entry. Lastly, the Mechanics’ View allowed mechanics stationed at the waiting area to promptly attend to recorded downtime incidents, helping drive efficiency on the manufacturing floor.
Case Study: Enhancing Operational Efficiency with PowerApps
Ardent Mills, a leading flour-milling and ingredient company operating across North America leveraged Microsoft Power Platform to navigate some of their operational challenges. Manual processes and lack of real-time reporting capabilities posed issues to operational efficiency and quality control across multiple plants.
The Challenges:
- Manual data entry tasks were burdening quality managers and lab technicians, leading to inefficiencies in quality control processes.
- Lack of real-time reporting capabilities hindered data-driven decision-making, impacting the company’s ability to optimize processes swiftly.
The Solution:
- Development of the “Cross Check” app using PowerApps to streamline data entry processes for quality control.
- Seamless integration with SharePoint Online lists ensured data accuracy and reliability, enhancing overall data management.
- Utilization of Microsoft Power BI for insightful reporting on product testing results, empowering quality managers with actionable insights.
- Creation of additional apps, such as “Bulk Carrier Feedback” and “Vehicle Inspection,” to streamline processes in transportation and logistics departments.
Business Impact:
- Increased efficiency by reducing time spent on manual data entry tasks, allowing employees to focus on value-added activities.
- Real-time insights facilitated proactive decision-making and process optimization, resulting in improved operational efficiency.
- Enhanced collaboration among employees through a community of citizen developers, fostering innovation and continuous improvement.
- Preparation for future growth by transitioning to Dataverse as the primary data source and exploring advanced technologies like Lobe and AI Builder, positioning Ardent Mills for scalability and innovation.
Case Study: Automating Invoice Fixing Processes with Power Automate
Komatsu Australia, a renowned Australian manufacturer and supplier of equipment and services for various industries, faced challenges in processing high volumes of invoices manually. With over 52,000 invoices annually, the parts department struggled with the tedious and error-prone task of fixing invoices, impacting efficiency and productivity.
The Challenges:
- High volume of invoices requiring manual processing by a small team.
- Pressure on the team to handle invoices accurately and promptly.
- Delays in processing invoices could lead to purchase order variances and disrupt downstream processes.
- Prone to human errors in data entry and processing, impacting accuracy and reliability.
The Solution:
- Utilization of Microsoft Power Automate and AI Builder to develop an RPA solution for automating invoice fixing processes.
- Implementation of unattended automation to eliminate manual monitoring of emails and validation against purchase orders.
- Development of Microsoft Power Automate cloud flows for retrieving and processing invoices, along with AI Builder document processing for data extraction.
- Integration with their mainframe system for invoice processing and archiving.
Business Impact:
- Automated processing of 1,200 invoices annually, resulting in efficiency gains of 300 hours per year for a single supplier.
- Reduction in errors by eliminating manual data entry tasks, ensuring data accuracy and reliability.
- 24/7 invoice processing capability, including weekends, improving responsiveness to overseas suppliers.
- Capacity freed up for the processing team, enabling them to focus on monitoring and managing exceptions effectively.
Case Study: Streamlining Business Processes with Microsoft Power Platform
Hexion, a global chemical company has been leveraging Microsoft Power Platform to enhance its core business processes. The company focuses on creating innovative materials for various industries, contributing to a safer and cleaner world.
The Challenges:
- Need to streamline and automate core business processes.
- Desire for efficient solutions to capture and manage customer information.
- Transition from Salesforce to Dynamics 365 Sales.
- Requirement for a cost-effective, customizable, and integrated solution.
The Solution:
- Utilization of Microsoft Power Apps and AI Builder to develop solutions for capturing and managing customer information.
- Adoption of canvas apps and Microsoft Power Automate flows for process automation.
- Integration of Dynamics 365 with Power Platform for seamless data flow and automation.
- Development of custom apps for IT-governed processes such as document sharing and team setup.
Business Impact:
- Efficient scanning of business cards and capturing of customer information directly into Dynamics 365 Sales.
- Reduction in reliance on third-party solutions, resulting in cost savings and increased flexibility.
- Quality and consistency of data improved, leading to better classification of leads and opportunities.
- Enhanced user experience with the use of canvas components in Microsoft Power Apps.
- Automation of IT-governed processes, including user access requests and team provisioning.
- Orchestration of core business processes across various departments, improving operational efficiency and performance monitoring.
Case Study: Streamlining Inventory Management with Microsoft Power Platform
Electrolock, a leading provider of insulation products sought to enhance inventory management processes for themselves and their customers. Facing competition with digital solutions, the company aimed to win bids by offering a user-friendly inventory tracking system.
The Challenges:
- Cumbersome process of tracking inventory using Excel spreadsheets via email.
- Need for a digital solution to compete effectively against competitors.
- Requirement to track inventory usage, create purchase orders, reconcile inventory, and record revenue accurately.
The Solution:
- Utilized PowerApps canvas app with data stored in Microsoft Dataverse for Inventory Management.
- Designed a user-friendly mobile app for customers to track and pick inventory items on manufacturing floors.
- Integrated with their ERP system for accurate recording of revenue and seamless communication of purchase orders.
Business Impact:
- Simplified and automated the inventory recording process for floor technicians using mobile devices.
- Enhanced accuracy and timeliness of inventory data, reducing manual entry and rework.
- Streamlined the reconciliation process, from listing inventory to drafting purchase orders and sending invoices.
- Improved tracking of inventory sent to customers, facilitating better inventory management.
- Enabled reporting functionalities for insights into purchase orders, inventory usage, and replenishment needs.
Embracing Tomorrow: A Glimpse into the Future with Microsoft Power Platform
Businesses, including those in manufacturing, are increasingly turning to low-code/no-code solutions like Microsoft Power Platform to boost efficiency. Yet, these solutions aren’t just about cost-cutting—it can also enhance workers’ lives and benefit society. In manufacturing, these technologies can help tackle key business challenges, improve employee well-being, and reduce the environmental impact of operations by minimizing errors and optimizing resource usage.
These technologies don’t just benefit workers’ health and the environment; it also raises living standards by fostering innovation and improving product quality. Moreover, it creates new job opportunities, particularly for people with disabilities. However, it’s crucial to take a human-centered approach to digital transformation supports workers rather than replacing them.
By embracing this approach, businesses can strike a balance between efficiency and well-being. Technologies like Microsoft Power Platform augment human abilities rather than replacing them. They assist with decision-making and streamline processes, while humans continue to play vital strategic roles. Ultimately, adopting a human-centric approach ensures that technology serves to enhance workers’ lives and drive positive societal outcomes.
Keen to learn how to eliminate inefficiencies within your business with Microsoft Power Platform? Join the second edition of Power Up in a Day, our complimentary, 2-hour, hands-on masterclass that’s open exclusively to participants from the Americas on 28 March 2024: https://us02web.zoom.us/webinar/register/4417097994388/WN_lpHZKqCnRgi-DehbBxqWJA#/registration
- Navigating the manufacturing maze: Current and future frontiers
- Unleashing innovation: The Power Platform's impact on manufacturing excellence
- Case Study: Enhancing Operational Efficiency with PowerApps
- Case Study: Automating Invoice Fixing Processes with Power Automate
- Case Study: Streamlining Business Processes with Microsoft Power Platform
- Case Study: Streamlining Inventory Management with Microsoft Power Platform
- Embracing Tomorrow: A Glimpse into the Future with Microsoft Power Platform
Subscribe to our blog to know all the things we do
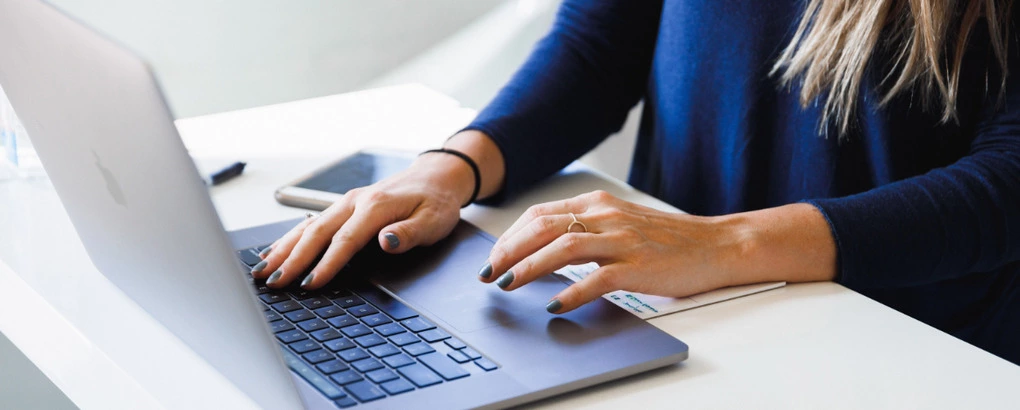