In this three-part blog series, John Broadbent, External Consultant at Fortude, explains how F&B manufacturers can do more with less while transforming business processes and services using digital technologies such as Industry 4.0.
In the first two parts of our three-part blog series, we touched on moving from ‘open’ to ‘closed’ loop manufacturing and how digital transformation (DTx) and Industry 4.0 can help the F&B sector ‘do more with less’. This final installment in the blog series outlines the staged approach that leads to the realisation of the Industry 4.0 vision.
Setting the foundation for your Industry 4.0 journey
• Computerisation
• Connectivity
Computerisation means having manufacturing equipment that is controlled by modern systems such as programmable logic controllers (PLCs), which contain the program that runs the machine. Modern equipment uses mainstream brands of PLCs, from global vendors (such as Siemens, Rockwell, Omron, Modicon etc) and are often capable of being connected to factory IT networks, via on-board Ethernet modules. These provide access to important internal information that can be viewed via real-time performance dashboards.The second foundational step, connectivity refers to the process of linking multiple equipments’ PLCs to the IT infrastructure, as well as other elements that come under IT’s remit to ‘deliver stability while enabling innovation’. These elements include switches, firewalls, WiFi, LANs, WANs and cyber-security.
Without both these foundations in place, we might have a factory network but we would not be able to easily extract data, or we may have PLCs with network capability, but no IT infrastructure to take advantage of it!
The Industry 4.0 lifecycle
Once these foundations are in place, we are ready to commence the Industry 4.0 journey. After 10 years of global adoption, the transition to Industry 4.0 is now a well-defined and well-documented path. There are four macro steps, which can be viewed as:
• Visibility
• Transparency
• Predictability
• Adaptability
Visibility, or being able to ‘see’ what’s happening on a production line, can only happen when the previous precursor steps are in place. We must be able to read information from our equipment’s control systems, which requires both computerisation and connectivity.
Imagine the speedometer in your car indicating you are travelling at 60km/h, this indicator, allows you to ‘see’ your speed. Now imagine you are in a 40km/h school zone, suddenly your 60mk/h has context, so transparency provides us with a reference to ‘understand’ what it is we are seeing. That same 60km/h example would have different consequences, if we are on a German autobahn, with cars passing us at 220km/h! Once we progress to the 3rd level of maturity, predictability, manufacturers can be confident about the accuracy of the information we are collecting and use the historical data to ‘prepare’ for what might eventuate. In the context of the car analogy, this would mean that we see the upcoming change in speed zone and adjust our speed before we get there. Finally, we now have enough confidence and history to automatically adapt to changing conditions, so we can ‘optimise’ our process. If we were to consider the car analogy again, we would compare it to modern cars which can now adjust its speed automatically to compensate for road speed changes or traffic conditions. The image below shows this progression:In summary:
• Visibility allows us to see
• Transparency helps us understand
• Predictability prepares us for upcoming events
• Adaptability allows us to optimise processes before issues occur
Let’s take the example of a food and beverage manufacturer who is running a filling or production line which has an inline checkweigher at the packaging end to ensure that every product leaving the line is the correct weight.
Visibility (See) – If we can connect our checkweigher to show us real-time pack weights, we can see what is happening in the process.
Transparency (Understand) – If we can display the target weight (setpoint) we now have context, so we might also be able to get useful information like over-and-under-weight reject counts.
Predictability (Prepare) – If we are charting pack weights on a Statistical Process Control (SPC) chart with a proper sampling regime, we can monitor weights to confirm whether our filling process is in control or not. If we ‘see’ that we are heading to a reject situation, we can alert an operator to make a change to the upstream filling process.
Adaptability (Optimise) – Rather than alerting an operator, the checkweigher monitoring system automatically adjusts the upstream process, without human intervention, thereby adapting to changing conditions.
This simple example illustrates how the four stages of Industry 4.0 naturally evolve, whether with a single system or an entire factory.
There are many manufacturers who are already reaping the rewards of investing in Industry 4.0 and are on their journey to maturity. If you have not started yet, we have a decade of empirical evidence that points to a healthy return on investment with the adoption of Industry 4.0 technologies.
What are you waiting for?
Related Blogs
Subscribe to our blog to know all the things we do
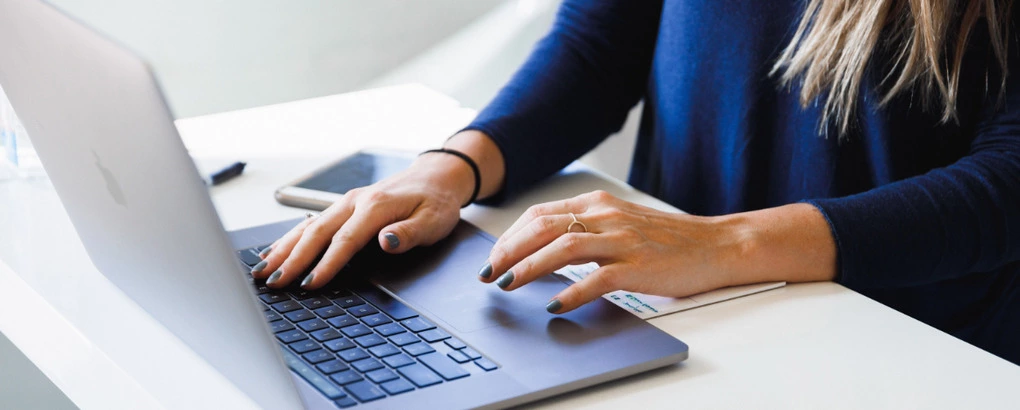