In my previous blog series Reset Retail: The pandemic and shifting customer expectations, I discussed how fashion companies could adapt to meet the challenges of the new normal.
For the most part, I focused on brands, but the same principles apply to fashion manufacturing. In this blog post, let’s focus on how manufacturers can adapt to the new normal by achieving visibility and collaboration with the right software.
Visibility
An ERP system (and again, my reference system is Infor CloudSuite Fashion) can provide the backbone for core processes related to manufacturing. Used correctly, it can provide the visibility that is demanded of manufacturers today.
Given below is a diagram of a typical fashion manufacturing business.
Figure 1: Fashion Manufacturing with Retail
Master Data Management (MDM)
Master data is the data that relates to all the entities and objects involved in your business. A style is a master data object, and the data relating to it will be the composition, color options, size options, images, SKUs, units of measure, and so on. Similarly, a supplier is also a master data object, and the data relating to it is information such as the address, payment terms, phone number, email address, bank details. Having those data maintained in a central repository, independent of orders, simplifies data management. Manually entering and maintaining data, every time an order is placed, can lead to a lot of errors. Instead, master data can be maintained in the MDM system, removing the need for cumbersome, repetitive data entry, reducing user error, and providing clear visibility. The data can be reused whenever necessary, such as for future orders on continuity styles or repeat orders with suppliers.
To make maintenance even easier, an ERP’s MDM system can be interfaced to systems such as CRM and PLM, if these are the initial systems in which the data resides. One could also create and maintain master data via EDI [Extend Infor M3/CloudSuite’s EDI capabilities with Fortude EDI] or easy upload tools.
Bill of Material (BOM)
A key master data element, the BOM, is like a “recipe” for manufacturing a style. It contains a list of all the raw materials (RMs) needed as well as all the functions you need to do – like sewing and packaging operations. In an ERP, various bits of master data are linked in a hierarchical BOM, together with the quantities required of each bit. For example, Style A needs 1.4 meters of fabric B and two of button Cs. If an order for 1000 units of Style A is placed, the system uses the BOM to calculate how much fabric B and button C is needed. It is also used for determining product costings.
The key takeaway here is that a good MDM system means transparency. A RM cannot be swapped for another without changing the BOM and recording it in the system.
Material Requirements Planning (MRP)
I am a massive fan of MRP; I think it is the engine that drives all the magic of an ERP. First, set up the master data, including styles, RMs, BOMs, vendors, lead times. Next, place orders or forecasts (again, these can be interfaced, EDI’d, or uploaded, no need for manual keying in). Press the shiny MRP button, and the system does all the production and procurement math for you.
It looks at all the demand and supply in the system:
- Stock sitting in warehouses, both finished goods and raw materials
- Manufacturing orders and purchase orders expected to be received and when to expect them
- Customer orders and forecasts that were placed previously and the delivery dates of those orders
It then calculates how much should be bought, how much should be made, and for what dates. It is extra clever because it looks across the different levels of the BOM and does this magic not just for the top level, which is the style, but also for the lower levels, the RMs.
It can be configured with all manner of bells and whistles such as assigning suppliers and prices, considering minimum order quantities, and considering approved product substitutes.
Manufacturing
MRP calculates how much to make by generating Order Proposals. The entire manufacturing process – including work order operations, subcontracting, value-added services, and packaging – can be planned and carried out by converting these proposals into Manufacturing Orders. This process ensures visibility and easy tracking throughout the manufacturing process, including subcontracting.
At every point in the process, you have complete visibility of who has handled a product, what has gone into its manufacture, and when it is due to be ready for delivery. You even know which Order Proposal was used to create the Manufacturing Order. Basically, you can trace the process back to the very beginning.
It is also possible to perform capacity planning, which allows for a smooth running of your manufacturing facility, leading to fewer issues and delays.
Allocation
The allocation may not seem like a critical area of concern for manufacturers. Often, when working with brands, the manufacturing process is make-to-order. The one-to-one relationship between the order placed and the goods manufactured does not warrant sophisticated fair share allocation rules. However, with the increase of omnichannel and drop-shipping, manufacturers need to have fluid and adaptable allocation systems that can deal with customer-driven, allocation, and delivery destination changes. The allocation module within an ERP allows for such flexibility while still maintaining the traceability of the supply chain from RMs to end-customer.
Business Intelligence (BI) and Analytics
It is wonderful to have an ERP system that captures every function that you perform in your manufacturing business. But all that data is truly pointless if you cannot access, process, and analyze it at will. This is where BI steps in. Infor Birst, which is such a system, interfaces to the ERP to collect all its useful data and then presents reports and analytics that actually provide a window to the awesome data. Furthermore, BI systems can pull data from different systems and present them in consolidated reports.
The increased visibility will also help with sustainability policies that will be crucial across all aspects of the fashion industry in years to come.
Collaboration
Figure 3: ION Desk workflow interface
Most ERPs focus on an enterprise and the functions within it. As social media gained popularity, ERPs were enhanced to include collaborative platforms that allow for easy communication, data sharing, and workflow management across various departments within an enterprise. Infor Ming.le is such a platform. It allows users across the organization to chat, share documents, assign tasks, and so on. Instead of generating copious reports that are sent from one department to another, cross-departmental workflows can be set up with notifications and alerts in place.
But still, more is needed! Not everyone works within the same organization. We need inter-enterprise communication and collaboration for brands, customers, suppliers, manufacturers, shareholders. Everybody who touches a part of the complicated fashion supply chain may need to communicate and collaborate with another part of that same supply chain.
Source: Infor | Optimize your supply chain network with Infor Nexus
Networking platforms, such as Infor Nexus, provide such functionality. Brands can log in directly to approved modules of a manufacturer’s ERP system and provide updates on order dates and quantities. As the data is now in the ERP, it can trigger the notifications and alerts mentioned above within the organization. Huzzah!
Keeping Global Manufacturing Alive Through the Right Technology
It has been a tough year. Global supply chains have been devastated. What does the future hold? Who can tell?
Regardless, we can survive. We can look back at the last year and see what worked and what did not. Visibility and collaboration across the fashion supply chain could mean the survival of its global and cross-cultural elements, elements that account for a significant portion of many developing countries’ GDP, providing millions with employment, food, and security. It might seem a decadent extravagance at a financially stretched time, but investing in the right tools in the right areas may just be what keeps cross-cultural manufacturing alive in the decades to come.
Written by
Related Blogs
Subscribe to our blog to know all the things we do
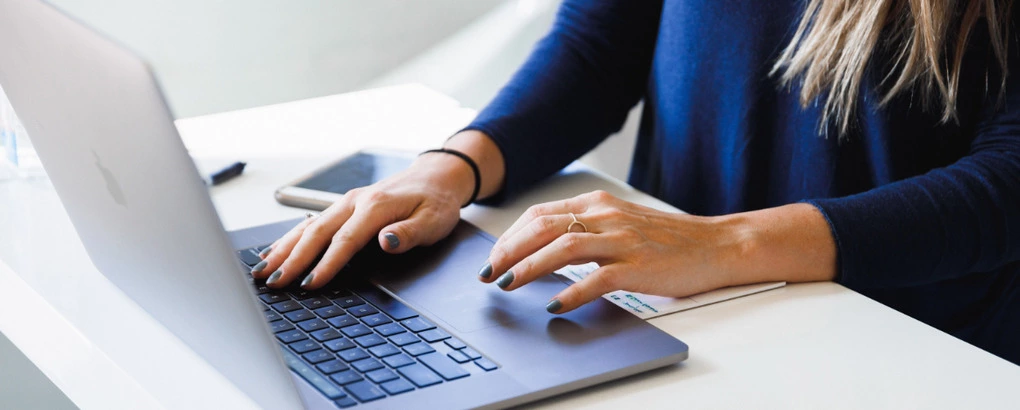